For the better part of the past seven years, Dustin Balton has worked as a project engineer and project coordinator at MEP firm, Holstein White (HW). In this role, Balton is part of the Mechanical department at HW, specializing in the design of the Mechanical, Plumbing and Fire Protection systems.
Balton coordinates the team of project engineers and drafters on any given project and serves as the interface between his firm and its clients. As the go-to Archicad/BIM guru in the Mechanical department (colleagues of his fill a similar role in HW’s Electrical department), Balton implements company standards for the firm in terms of Archicad use. The PA-based firm integrates Archicad into its workflow, setting itself apart from other firms in the region. They were the MEP firm brought on by Archicad-firm, Kitchen & Associates to work on the Brook St. Lofts project recently highlighted here on the blog.
During the last four years, HW has been focusing on fully integrating Archicad and developing standards and templates to improve the firm’s ability to transition from other CAD platforms to that of Archicad. In terms of getting up to speed on implementing Archicad, as far as what Holstein White does, the changeover has been smooth.
Fully Collaborating in Archicad
Focusing on the essential part of the MEP firm’s role on any project helped fuel the decision to move toward Archicad. “We manage the mechanical, plumbing, and electrical engineering for a building – basically behind the scenes work. The key lies in being able to integrate and not be obtrusive. This highlights the need to fully collaborate with architects to not only make a system that is fully coordinated, but also does not take away from the artistic quality of the architect’s vision for the project.”
Prior to adopting an Archicad platform – some four years ago, Holstein White was still able to achieve a high level of coordination; however, with a deeper implementation of BIM technology through the use of Archicad, the coordination process has been simplified and expedited. The workflow to facilitate that collaboration and coordination with architects on other projects relied on PDFs and CAD plans of structural or architectural elements – overlaying them. Balton says the new set up is light years ahead and much more reliable and intuitive, making the coordination process much more seamless.
The ability to be in a file with the architect at the same time and being able to message them and have them pull up an area of a section view and share that view with us cuts down greatly on having to flip through multi-page documents to find a specific section view.
“Comparing where we came from to where we are now, it is vastly improved. The ability to be in a file with the architect at the same time and being able to message them and have them pull up an area of a section view and share that view with us cuts down greatly on having to flip through multi-page documents to find a specific section view. Sometimes you struggle to locate the area you are seeking. Having that full information at our fingertips has been very beneficial.”
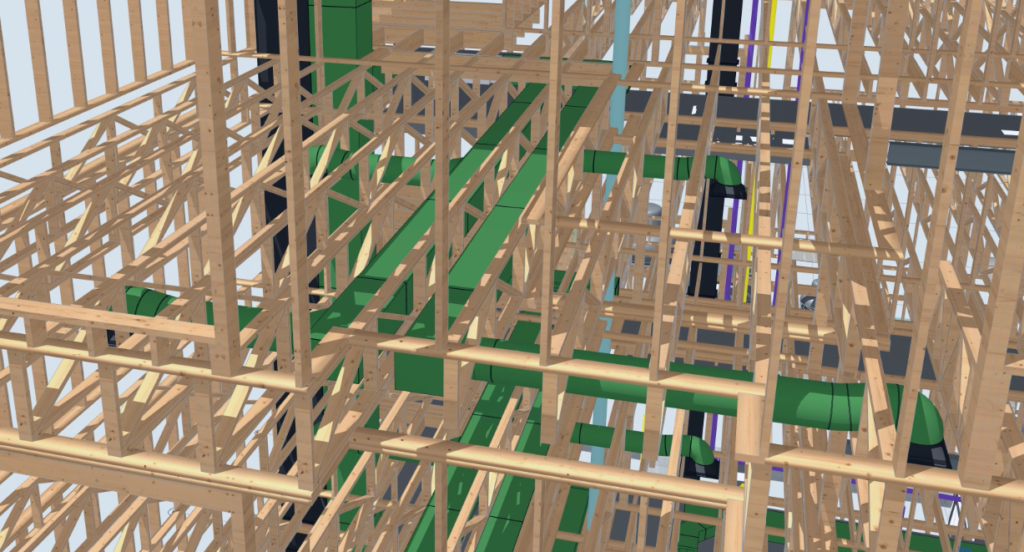
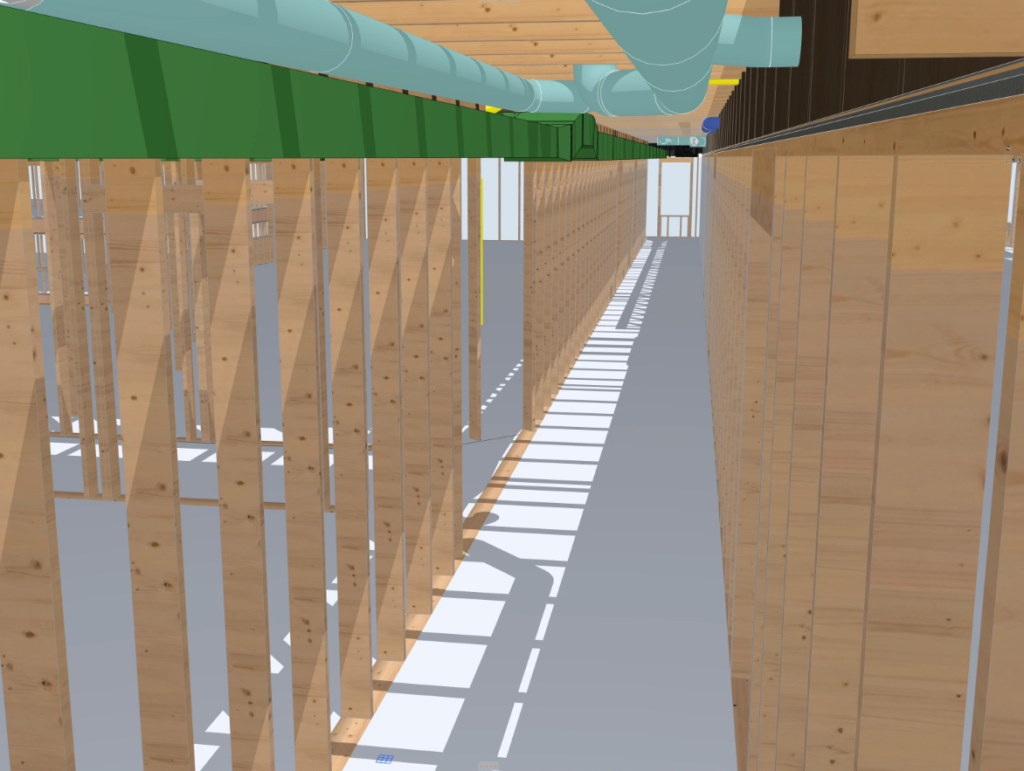
Teaming up during transition
Team members at HW adjusted to the shift to Archicad with project-specific protocols and an understanding about when to work in a 3D environment as opposed to 2D. Acclimating from one ingrained process to a completely different thought process took some doing. But, at this point Balton says the transition has gone well, with help from in-house trainings and seminars offered by Graphisoft North America (GSNA).
“When a new employee joins the team, we have them take pre-established training classes. Most have been modeled off seminars GSNA offers. In addition, we have a template that goes through a project piece by piece and shows our engineers and designers how to use the software, bringing in the backgrounds that we need and cleaning things up and setting up our standards.”
HW has developed a best practices document that serves as a training guide for drawing set-up and 2D permit submission documentation, which is the bulk of the workflow. All employees at HW are also trained in 3D drafting, but there is a specialized 3D team that will hop into a project when needed to further train and assist in 3D documentation. Balton says this specialization helps keep things tidy and further develops the 3D documentation skills of the company.
“Not everybody in our office is doing 3D work at any given moment as there are multiple projects that do not demand this level of documentation. All employees at HW have the skills and tools to provide 3D design services and we also have a team that specializes in 3D design that is available to train and assist where needed.”
All in on Archicad
At this point HW exclusively uses Archicad on all projects, which integrates with other BIM and cad platforms utilized by many of their clients. In cases where the project files do not contain all the details found in an Archicad model or a BIM model, Balton says the team does have to fall back on their previous method, which serves as a reminder of how much more detailed and efficient they can be using an Archicad model or a BIM model.
“While files need to be brought in from other platforms on larger projects, for example, the firm has models established with BIM information in it. On projects at a scale where we need to see parts of the building in 3D that don’t have that information, it is a little tougher – maybe it is an existing building where they might not have drawn in all the structure or something like that. It is difficult to go from having all that wealth of information to not having it, especially when you are trying to run a large 30 by 20 duct down a hallway. You do not have every piece of information on what the structure is and where the ceilings at, or the lights are. It can certainly be difficult.”
On the Brook St. Lofts project, and other BIM projects, HW has none of that difficulty. Readers of the blog will recall details about how quickly issues could be resolved. Balton shared his view on how architectural, structural and MEP worked together to coordinate throughout the building.
“We did some coordination live with the electrical bus duct that we were trying to route up through the building. It was coming through a parking garage, we had to squeeze in between parking spaces, and there were lots of moving parts with where there were structural beams that had to be avoided. Jessica, an architect at Kitchen & Associates, was able to block out the space and we were able to take over and move it where it worked on our end. Essentially we saw the solution at the same time, rather than two of us sitting there and thinking something might work and then going and asking the structural about it, and seeing if they’re able to make it work on their end. With all parties being in the same software at the same time, and being able to say, ‘Hold on, that’s not even going to work at all. Let us not chase our tail but try something different.’ I think that was really what was beneficial.”
That’s just one example of many Balton adds, “Similarly the ductwork coming up through the roof, where there are larger joists – we had to route through open webs of those joists. That was also a big moment where Jessica, and I believe it was either Patrick or Jake from Riverstone, we were all on the phone together trying to figure that stuff out, too. There were multiple instances where live coordination was occurring all over the project. It wasn’t an uncommon occurrence; it was happening continuously throughout the design process.”
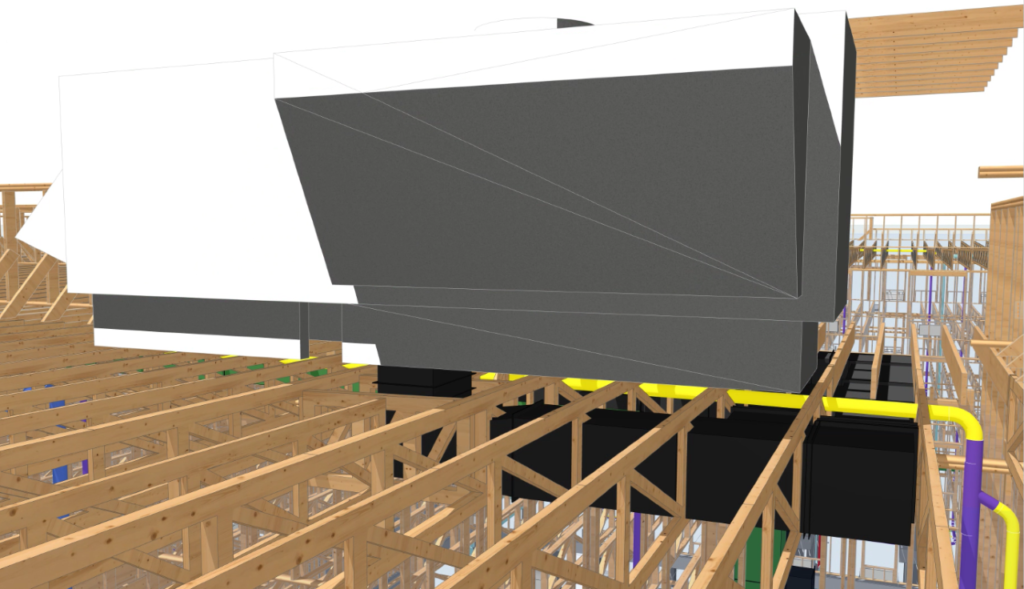
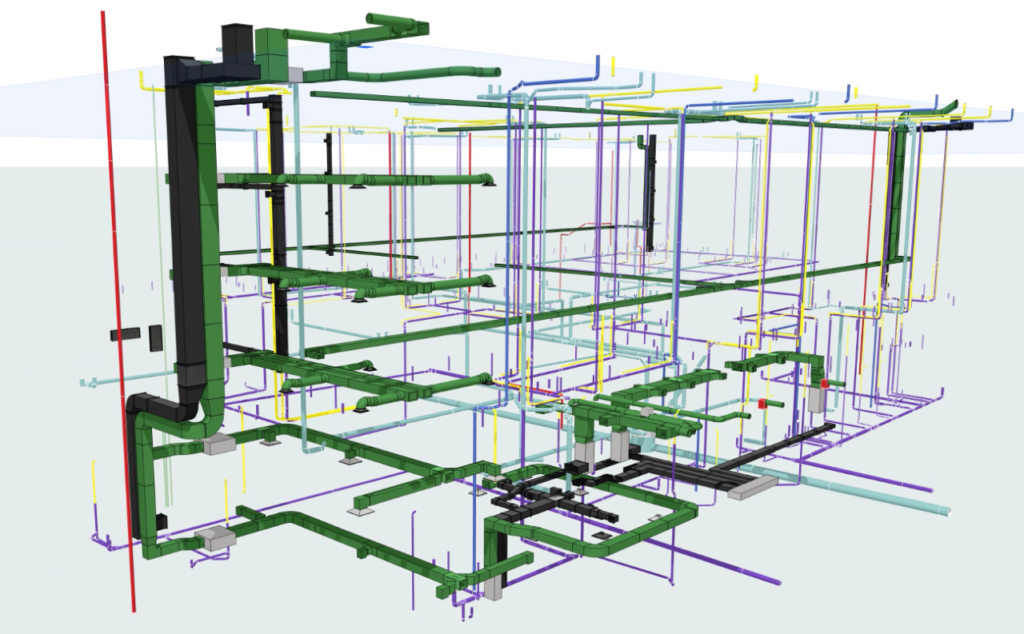
Moving on for more work together
That coordination took some setting up in the beginning, as it was the first time HW had worked with Kitchen & Associates in this manner. Establishing protocols, getting onto the K&A server, and adjusting to K&A’s standards has paid off because the teams are collaborating again on a 66-unit residential project for low-income people who are 55 and older called Hoffman Pavilion.
MEP firms using Archicad are not always involved in the early design phases, as they are typically brought in on a project later than the architect, and sometimes later than the structural. Balton characterizes the early work done at HW as narratives, putting together a scope of work written report explaining what they intend on doing system-wise, and the preliminary sizing of incoming services, maybe doing small sketches of areas that might be taking up a lot of space, whether it be a large electrical room or an incoming services room for domestic water or fire protection services.
“On Hoffman Pavilion, our second project with K&A, we were brought in earlier than usual in terms of having access to the model. And while we were writing that narrative, we had access to the model and were able to check that things fit ahead of time, so we are speeding up the process a little bit and streamlining things. Once we started to design, there was less back and forth, less coordination efforts and overall less issues that arose because we were able to already get our heads wrapped around the building earlier in the process.”
Once we started to design, there was less back and forth, less coordination efforts and overall less issues that arose because we were able to already get our heads wrapped around the building earlier in the process.
Hoffman Pavilion, a senior housing residential facility located in New Brunswick, NJ is about halfway through the design phase. HW currently awaits a meeting with the ownership team to review drawings prior to moving into the CD phase. Balton says this project has been clicking along quickly and is scheduled to have permits issued within the calendar year.
Ready to take on more
In the wake of the Graphisoft Building Together digital event, HW has put the word out that they are open to working with architects in Archicad and have already made significant inroads on projects going forward. Balton says many architectural firm principals are viewing the initial hiccups that may come with adopting this new collaboration on MEP as a training investment, an investment in efficiency.
“We have seen how it will pay off in the end. Needing to coordinate with your MEP firm, is always going to be there, so why not take the lumps early and develop a working relationship that you can hit the ground running after that. Look at the evidence on our first project versus the second project with K&A. The first project with them, we deployed some extra resources to make sure we made the transition work seamlessly and likely spent more time and effort than we originally had anticipated. But now we’re already seeing the benefits on the second job because we are immersed more in their way of designing and have adopted some of their standards. And I think the process has already been streamlined, just in terms of from one project to another. We can attribute it, at least in part, to the ease of how Archicad works, in my opinion.”
Given the success on these two projects, when asked if more MEP firms will move towards BIM or 3D modeling, Balton certainly agrees, but in-depth calculations, code research and interpretation, utility coordination and preliminary, space-grab coordination in 2D will always be necessary to set the stage for success and streamline the process.
“I see the merits in 3D work as it pertains to MEP, but at the end of the day, the foundation has to be solid for the 3D to even resonate. We must have our calculations done properly. There is so much that we as engineers must do that is not seen before we get to that level of documentation. When we first get involved in a project, we focus heavily on calculations and preliminary coordination, so working in 2D is sufficient. As the project progresses that is when we move into the fine details and model key areas and elements in 3D. We are able to do this at that point because we set the project up for success with a strong foundation focused on engineering calculations and preliminary coordination.”
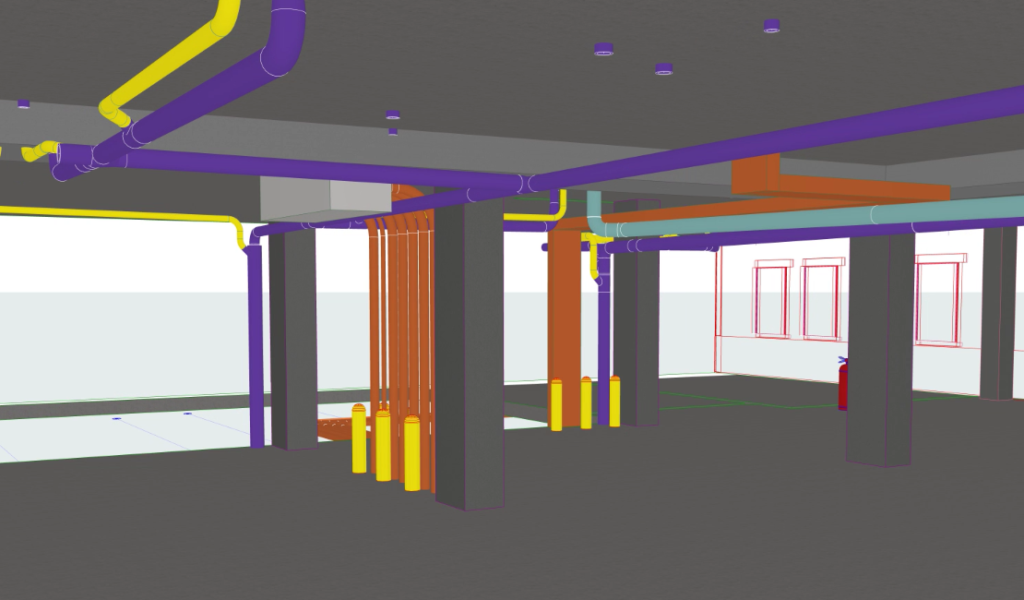
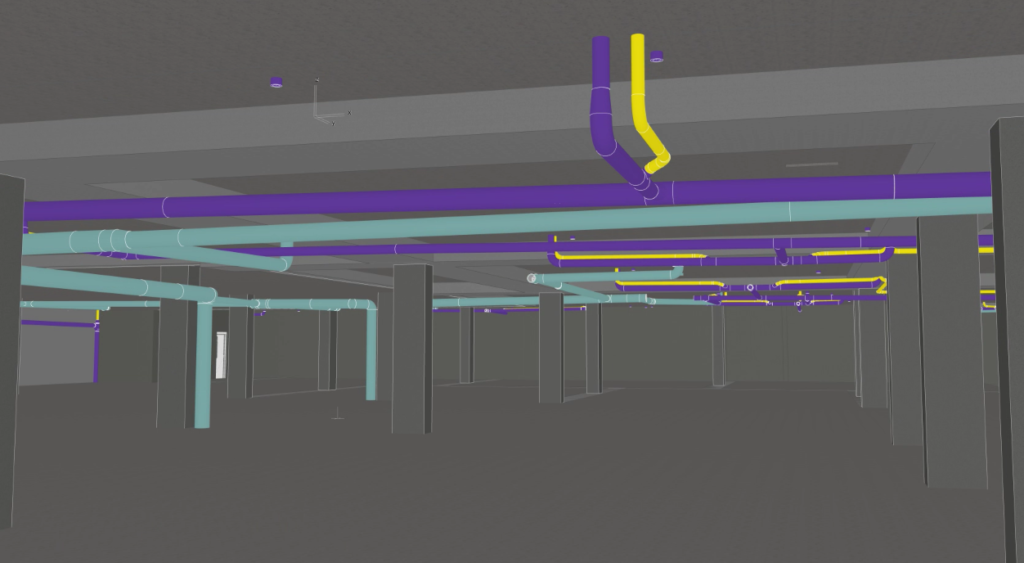