February 17, 2021
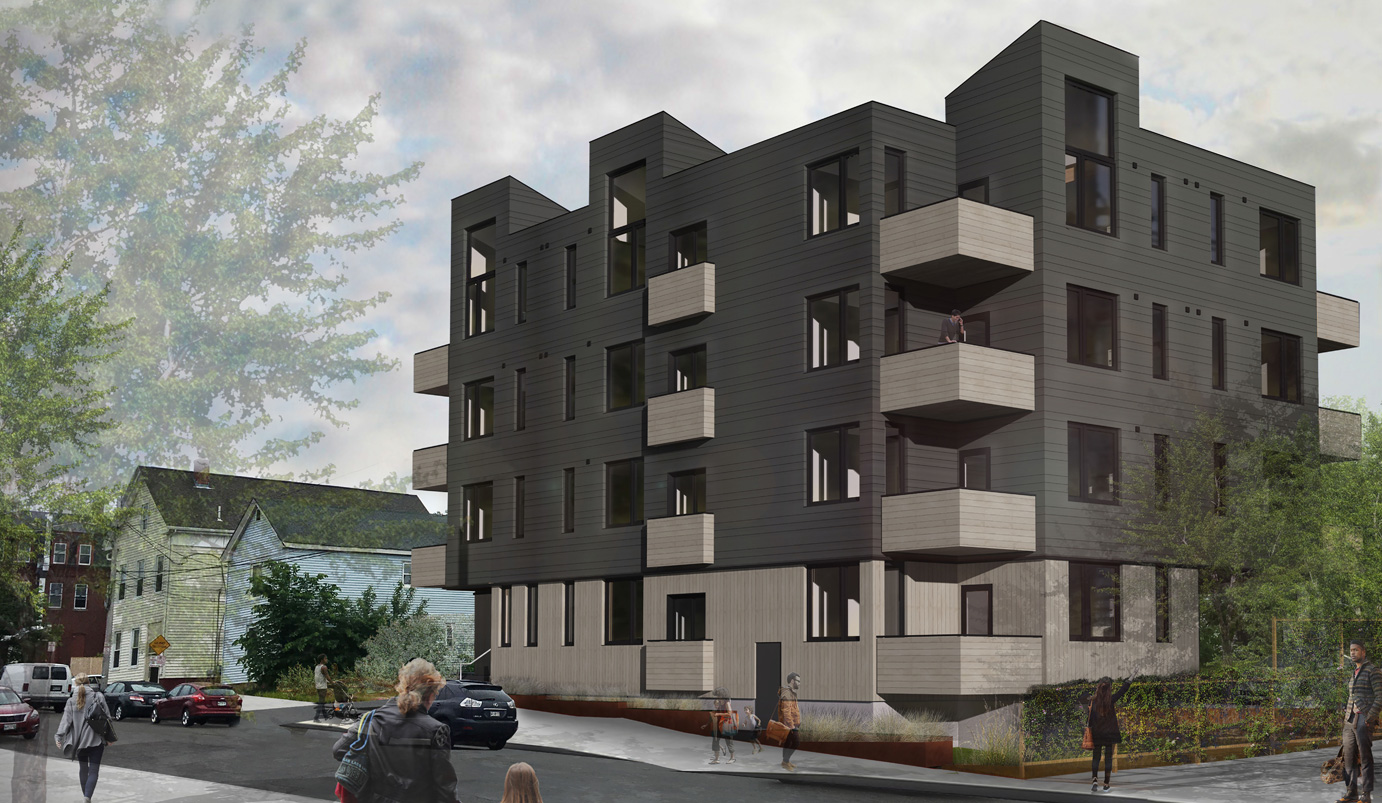
In this article, Kaplan Thompson Architects discuss their ‘Parris Terraces’ project, an award winning complex of affordable, single-bedroom apartments.
Kaplan Thompson Architects (KTA), a unique, Archicad-using, Portland, Maine-based firm routinely pushes themselves to expand the ways in which they design residential projects with Archicad. That dedication to innovation and excellence has resulted in the firm receiving awards for excellence from AIA Maine, and a 2020 Design Honor Award from AIA New England for their work on Parris Terraces.
Parris Terraces is a 4-story multifamily, sustainable, workforce housing project, with no state or federal subsidies. Workforce housing units provide market rate housing based on 120% of the area median income, a requirement of the city within this zone.
It was modeled in Archicad from start to finish.
Making the Most of a Small Site
Measuring 13,700 square feet, Parris Terraces is made up of 23 units. The site presented KTA with some challenges at the get-go, namely its size. Adam Wallace [Associate] of Kaplan Thompson explains.
“The site was a parking lot – the city would sell it only to a developer who would provide affordable/workforce housing. As architects, we knew we needed to create a super dense, high efficiency ratio for the building. Our first obstacle was to test fitting all of the spaces, both interior and exterior, on a really small lot.”
In order to achieve the desired one-to-one parking, Wallace says the firm opted for tuck under parking. Modeling in detail helped the team fine-tune the layout of the units and the layout of the building. Each unit measures around 400 square feet. All the units are one bedroom, so there are no studio apartments. Wallace says the team took an opportunity to have some fun with the units on the top floor.
On the top floor, we had some freedom to play with the roof line. We created what we called “roof pops” – which were little loft spaces.
Adam Wallace, Associate at Kaplan Thompson
“On the top floor, we had some freedom to play with the roof line. We created what we called “roof pops” – which were little loft spaces. From the outside of the building, those pops appear as an additional story with large tall windows placed high on the wall fill the space with tons of natural light.”
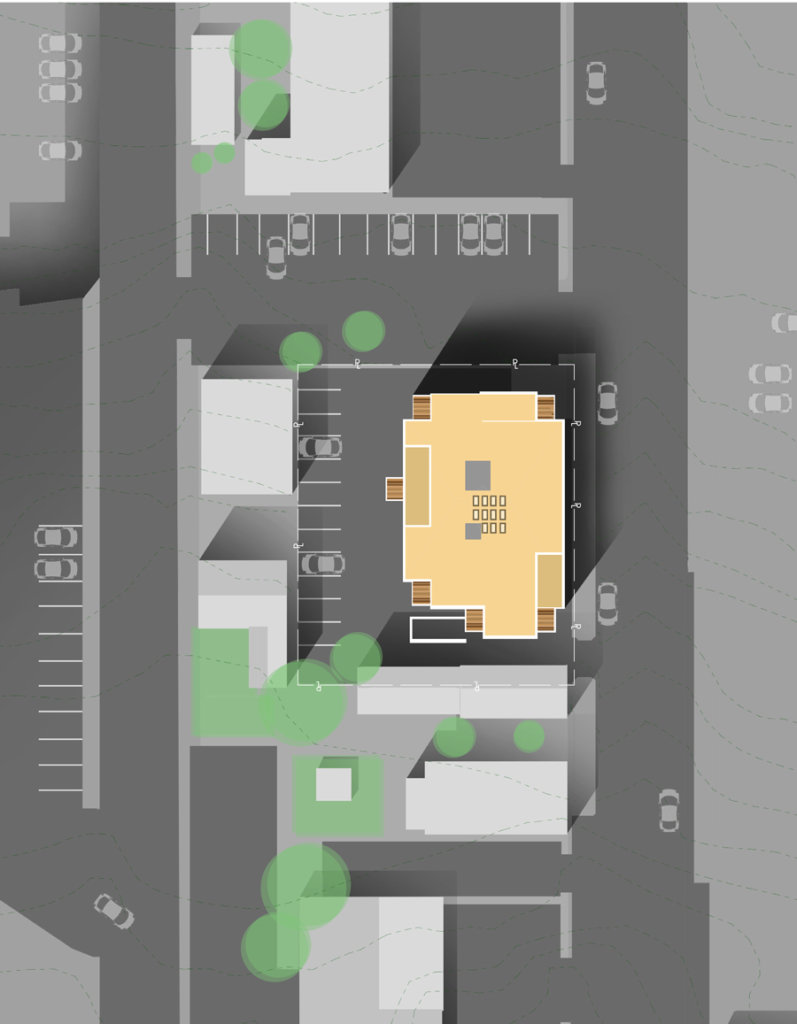
This diverting design addition allows for ladder that a resident could climb and space for a small office, reading nook, or sleeping loft. Just 70 square feet filled with natural light. Proof that the design worked could be drawn from the fact that all the units were sold before the building completed construction.
“The developer was super excited about being able to sell the units before we’d finished construction. The goal was to provide as many homes as possible that first-time home buyers could afford and still make the numbers work as an overall project.”
Fostering Financial Appeal
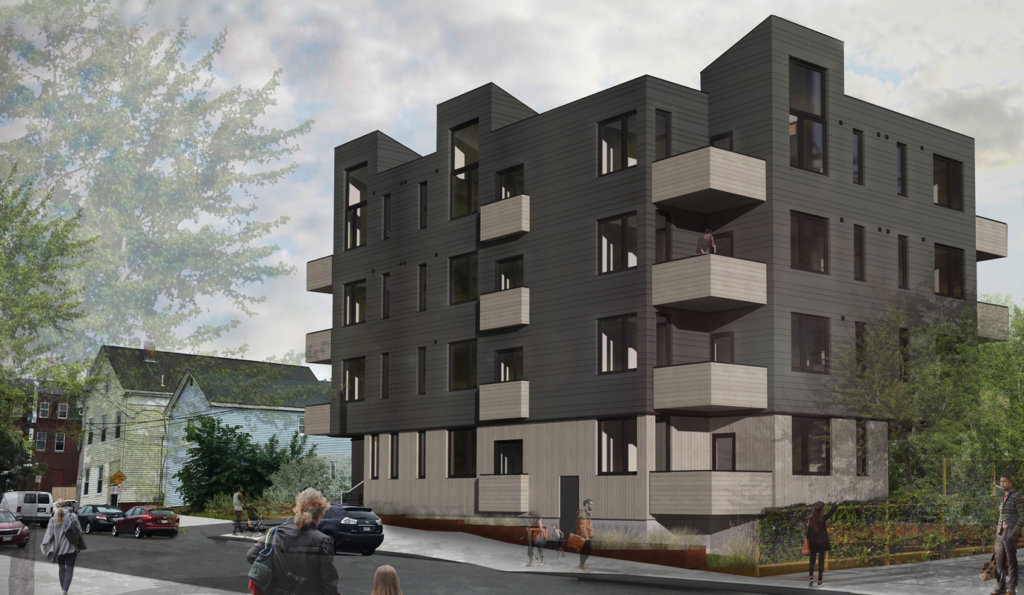
Wallace says another incentive for first-time home buyers was an agreement with a local bank that offered loans without requiring private mortgage insurance. This allowed first-time home buyers to secure a mortgage that at the time was lower than anything that could be rented in Portland. Now that the scene was set for a financially appealing scenario, the challenge fell to the team at KTA to make the units themselves appealing, despite their small size.
Wallace recalls the developer’s concern and says the team responded with a unique feature. “We kept asking ourselves the question ‘How great can we make these?’. The answer, in part, was giving every unit an exterior balcony and all but four have a private 8×10 deck outside. That feature instantly upped the ante, making the units more appealing.”
Bring on the Visuals
Archicad had a starring role in helping sell these units. Wallace says showing the design in 3D to the developer provided a huge benefit. It also helped when one considers a unique aspect of Parris Terraces. The building has no exterior shear walls. Structural Integrity, the structural engineering firm on the project was able to provide all of the shear strength for the building from the stair towers and a few select interior walls. This allowed for the exterior rigid insulation to be attached directly to the wood framing, eliminating an extra layer of plywood. The building has two inches of exterior rigid foam insulation, thermally isolating the structure from its exterior skin. It is a wood frame building with only one piece of steel located out above the tucked under parking.
Building the composites accurately in Archicad helped everyone visualize what was in the design.
Adam Wallace
“Building the composites accurately in Archicad helped everyone visualize what was in the design. This was a first for the engineer on a building this size with wood stair shafts and wood elevator shafts. It was also a first for the builder to work on a building without exterior plywood.”
Kaplan Thompson utilized the composites in Archicad so that they highlighted those elements clearly, also taking advantage of graphic overrides to demonstrate how the various layers connected at complex intersections.
“Archicad let us highlight different wall types by colors. We signified those distinctions on three or four additional sheets in the drawing set, so each wall type was assigned a different color. They could then be scheduled so that the builder would be able to price the project. With a look at the colored floor plans, they’re able to put a price per linear foot on a specific assembly.”
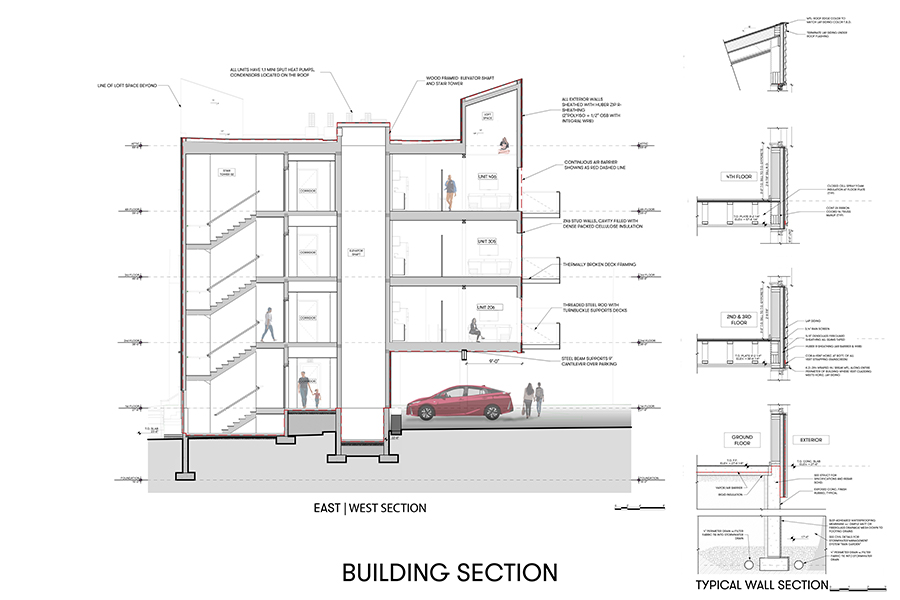
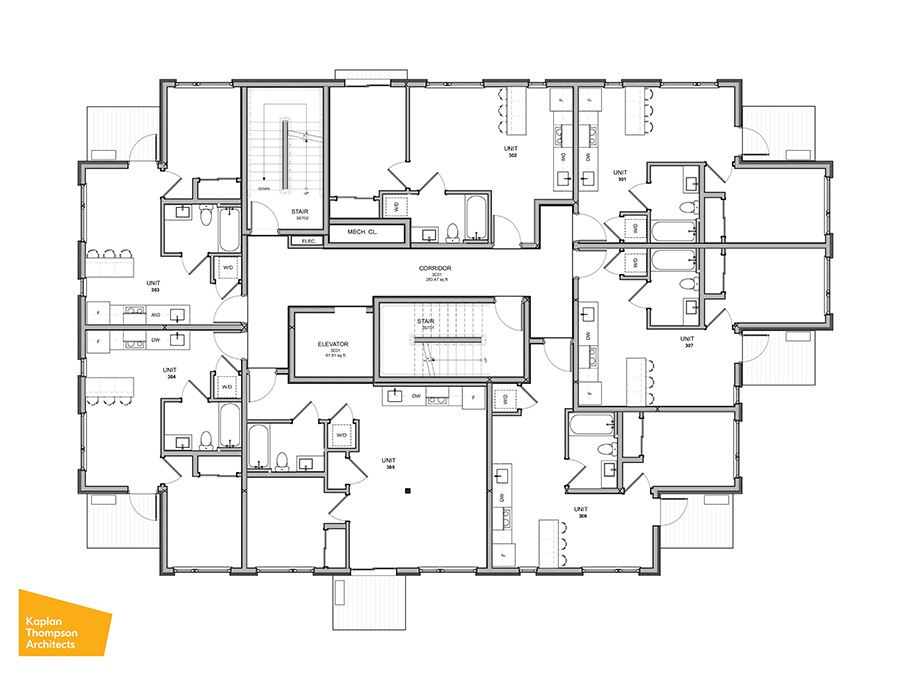
Seeing Sustainability, Streamlining Costs
Building composites and graphic overrides in Archicad worked to simplify understanding for the builders and streamlined cost comparisons for the firm.
“We scheduled all of those assemblies so at a glance, it was easy to determine, we have X number of linear feet of this wall type A and X number of linear feet as wall type B. This was fantastic for us to compare builders’ cost because you could evaluate accuracy for their exterior enclosure and all of the various interior partitions.”
Parris Terraces boast some sustainability features and energy efficiencies that merit mention. The project installed high quality fresh air ventilation systems in each apartment, which meant the exterior enclosure could be detailed to be exceptionally airtight, utilizing an integrated air barrier product that can easily be taped and sealed, around windows/doors, and all other conditions. The wall cavity installation was all densely packed cellulose. As a firm, KTA works to limit using spray foams on all projects as much as possible to limit exposing any of the nasty chemicals to the workers on site. Cellulose was applied to fill the stud cavities, providing R-values to achieve efficiency with a sustainable material.
“The units are heated and cooled with their own single tiny mini split heat pump. Most are located on the roof or on the balconies. The outdoor condensers can double as a small table, you can’t even really tell they’re there. The result is that with a 390 square foot unit running a 9,000 BTU heat pump, electric bills are around $30 a month.”
Meeting and Exceeding Modeling Challenges
Given that Parris Terraces was situated on a small lot, modeling everything in Archicad was very important. It ended up being key to making sure that it was all going to fit, downtown, on the edge of existing 1940s residential, three-story townhouses. In addition to providing views of how the building would fit in its neighborhood, the model helped determine that the building had adequate fire truck access the fire department required.
“Modeling everything on site included making sure the fire department could get at least one of their firetrucks on site. Modeling the location of the building on the site and then providing enough space for the firetruck to get in – we couldn’t just fudge that – especially since there is a residence that’s right next door to our drive aisle. Again, a tight spot that meant we had to model the balconies because they were close to that edge.”
Wallace says the firm also worked with Ransom Consulting as civil engineers to evaluate where storm water would drain. The tuck under parking lot and the one-to-one parking forced the paving of 92% of the rest of the site. Civil engineers developed a rain garden to filter the water that had ran across the parking surface, by a sequence of cascading tiers of planting beds that would remove unwanted contaminants in the water before it was released into the stormwater drains.
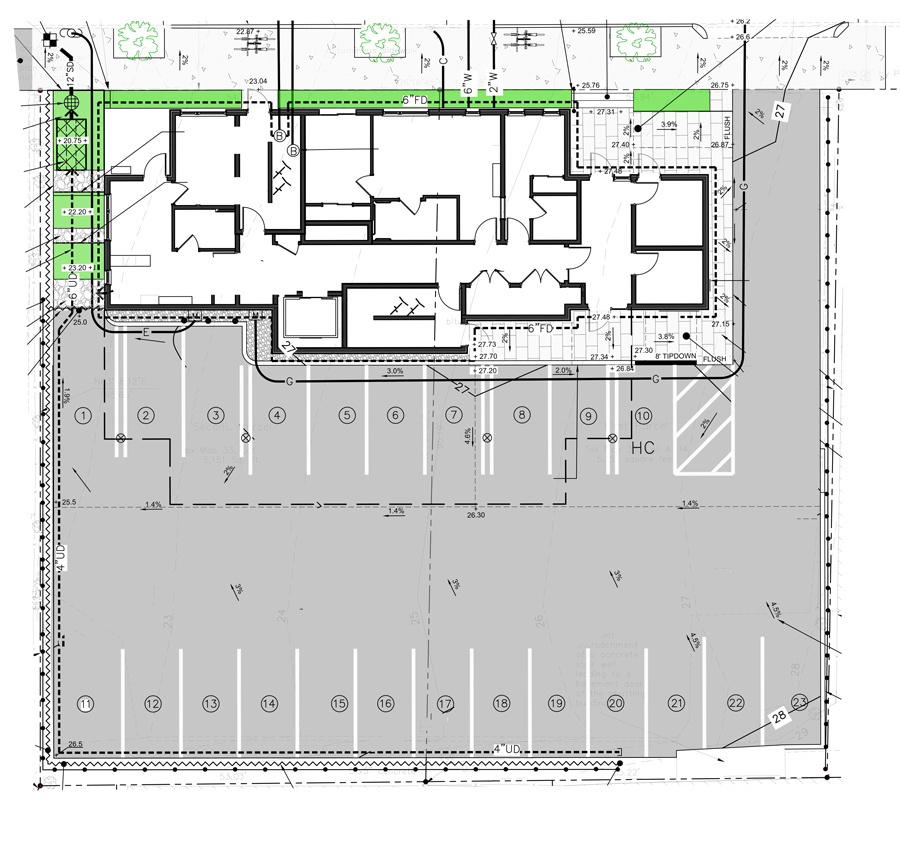
“Modeling that was a challenge. We put the site mesh in and matched the contours with the civil plan. We needed to also make sure an SUV would fit under the steel beam in the tuck under parking lot. In Archicad, we modeled from the ground up. From the rain garden up, to ensure elevations worked and then all the way up to the upper end of the site and to fit under that steel, it was great to see it all in 3D. It helped us see that we did not have to adjust the height of the ground floor which then makes the stair towers bigger, et cetera.” KTA used eastern white cedar from The Wood Mill of Maine for the cladding of the ground floor and all the balconies. Fiber cement clapboards were used on the upper floor.
Archicad at the Heart of Reliable IFC Exchange
Archicad helped us work out all our discussions with the engineer and the developer for how to deal with the loft spaces… It’s a very useful tool to be able to make changes and quickly show everybody in 3D what’s going on.
Adam Wallace
The firm employed IFC exchange for plumbing and mechanical. All the pipes were modeled. This building had virtually no duct work – but there was a question of how to get three-inch toilet drains down and across that steel beam from the parking area. During the submittal process when the firm gets shop drawings from the builder, it is their job to check and make sure that structure is where it should be and is not interfering with any major plumbing or mechanical element. Again, the Archicad model comes into play.
“It was important to model every floor joist, beams, and columns that were substantial so that when we’re going through the submittal process we can highlight right off the bat like where toilets are. If it had come up ‘Well, we may need to move this floor joist over six inches.’ Having all the plumbing fixtures in the 3D model was helpful because we could quickly see, oh, there is a plumbing pipe that’s going through this joist. Again, it’s a nice thing to be able to do from the model.”
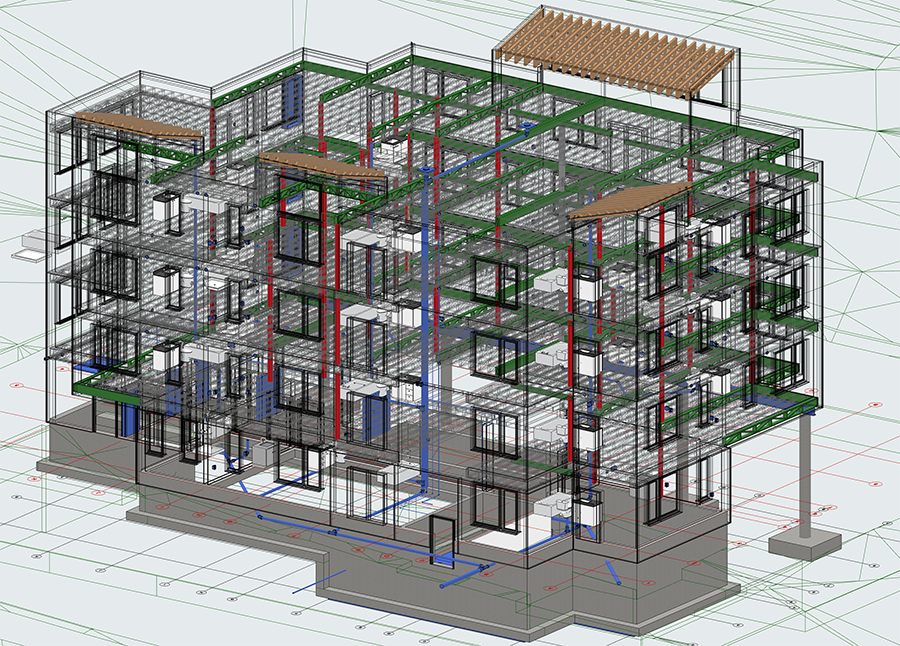
About Kaplan Thomson Architects
Kaplan Thomson Architects design new and renovated single-family homes, multi-family buildings, educational facilities, and restaurants across New England and beyond.
For more information visit kaplanthomson.com