The team at FORGE CRAFT works to fully embrace what they consider a responsibility as architects to push design ideas that address current conditions. Powered by Archicad, the Austin-based firm has developed a concept for Factory-fabricated and nimbly distributed method of standing up urgent care facilities when the situation demands it.
According to the firm’s press release, the CARE+CRAFT module, “…is a scalable and repeatable clinical treatment unit, premised on a unitized, self-contained patient room that can be factory fabricated and deployed in a multitude of configurations.”
When pressed to explain how this idea arrived with seemingly opportune timing, principals Scott Ginder and Rommel Sulit point to a routinely scheduled building systems’ charrette. It was because of ideas that sprung from those design discussions the firm began working on a “PoCo” (Post-COVID) white paper, addressing health concerns such as physical distancing in a micro-unit project and outdoor space access.
“Factoring the built-in design innovation lag time that goes along with major events like pandemics, I think we were ahead of the curve,” explained Sulit. Ginder adds, “We had looked for ways to address technical aspects, in collaboration with our mechanical engineers, about air exchange improvements that don’t sacrifice building efficiency.”
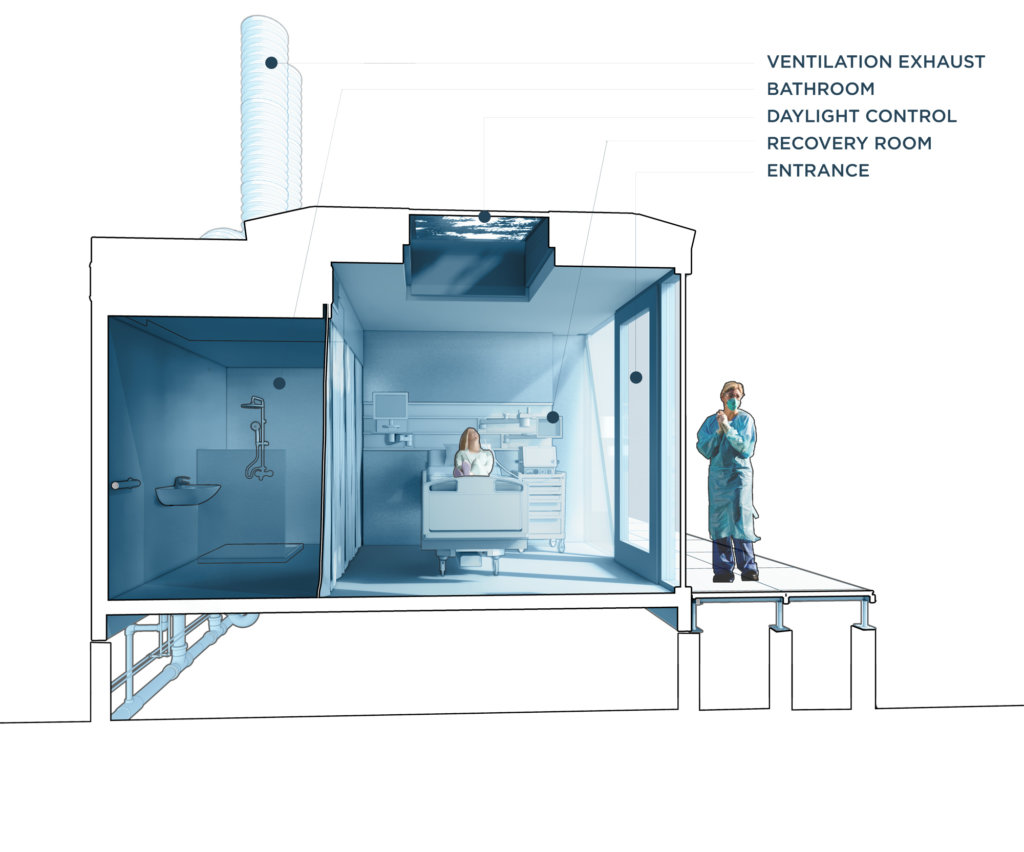
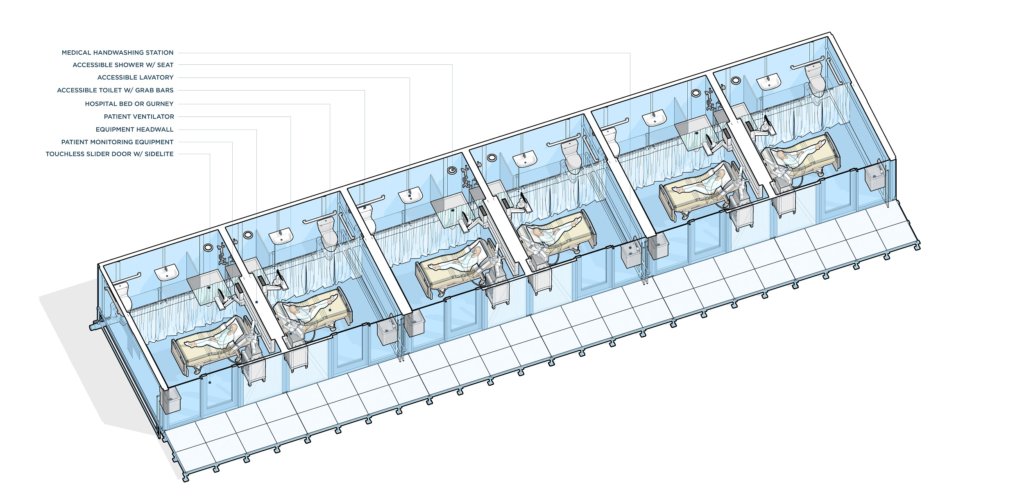
The Software
The founders of FORGE CRAFT chose Archicad as the firm’s software platform with an eye on being one of the firms responsible for the software’s advancement. Upon adopting the software platform for all projects, Sulit reports half of their staff demonstrated proficiency – which continues to grow amid a culture that fosters pushing the envelope of what can be done in the system. That commitment has paid off.
“We collaborate well even if another consultant is not using Archicad. Coordination with accuracy on highly advanced, detailed, technologically complex projects – especially a modular medical clinic like CARE+CRAFT, Archicad is all we need.”
An Archicad-centered workflow makes it possible for CARE+CRAFT to be quickly fabricated and deployed as a solution to the COVID-19 pandemic or other future global crises or disasters. Capitalizing on the firm’s comprehensive expertise in modular design and construction with the technical support of Archicad makes it possible to estimate construction and delivery of 300 patient rooms in a two-week period.
Quite the rapid response method.
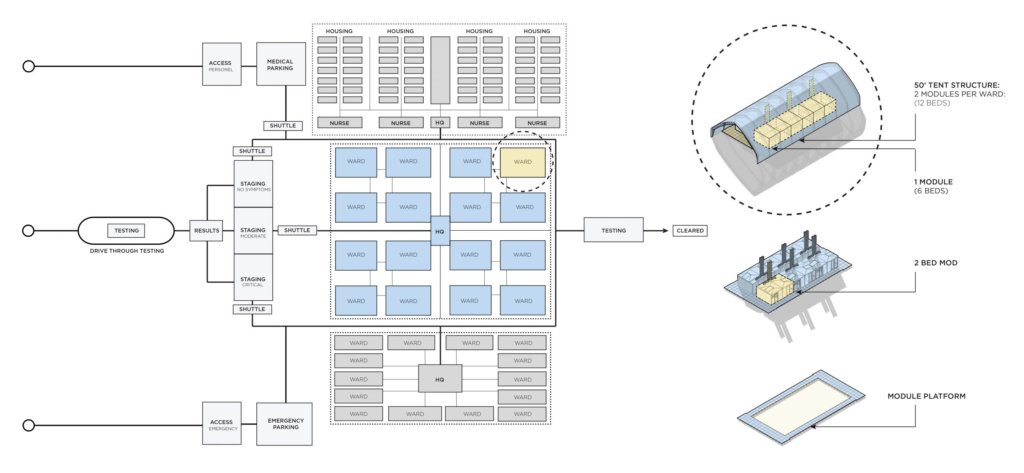
Cheatham Street Flats
Speeding up construction and promoting projects that would spur growth in the post-COVID era remains a focus for the AEC industry. Forge Craft stands ready with completed projects that demonstrate how modular design and construction could provide that. The firm has completed about half a dozen modular projects (many more non-modular) in the last four years, including Cheatham Street Flats, a 143-unit, 234-bed student housing mixed-use development.
This project demonstrates the firm’s innovation in progressive prefabricated modular design and construction methods. A normal project life cycle for a development of this size would be around 24 months. Ginder and Sulit say it took just 12 months to fabricate and set the modular portion of the building and some additional months to complete. An average time savings on most prefabricated projects would be about 40% faster – provided that the site-built contractors and trades commit and adhere to the established overall project schedule.
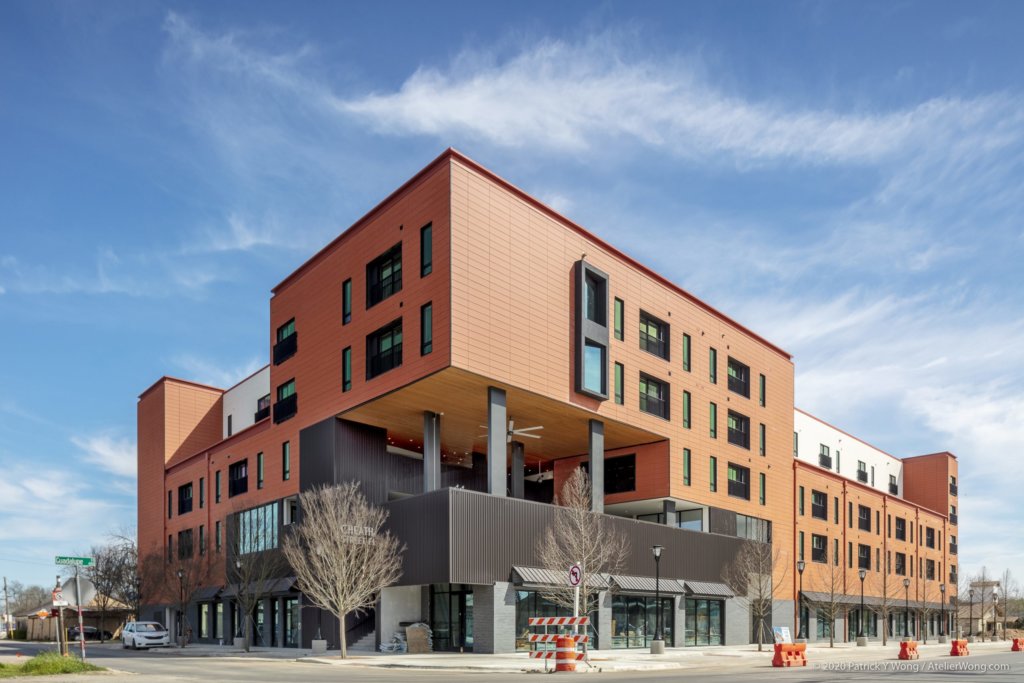
The building provides 143 residential units in San Marcos, Texas. The building construction includes a concrete podium separating the residential component from the parking and commercial spaces. Common space amenities & leasing office as well as approximately 190 parking spaces and 5,000 square feet of commercial ground floor shell space round out the facility.