Project Showcase
Data-driven BIM design delivers dynamic
exhibition space
Port Messe Nagoya First Exhibition Hall 1
Takenaka Corporation
Japan
Port Messe Nagoya First Exhibition Hall, Takenaka Corporation, Japan, takenaka.co.jp, Photo: ©SS Co.,Ltd., Mitsunori Aiba
Team
About Takenaka Corporation
Takenaka Corporation is one of the big five general contractors in Japan, known collectively as the Zenecon. With expertise in design, contracting and supervision of large-scale construction and engineering projects, the organization employs almost 8,000 people.
An Archicad user for 20 years, Takenaka has recently developed its ‘Design BIM Tool’ for all new construction projects. Using Archicad and Solibri together with OPEN BIM and AI workflows, the tool uses data-driven advanced model simulations and design verifications to help clients make decisions faster and more effectively.
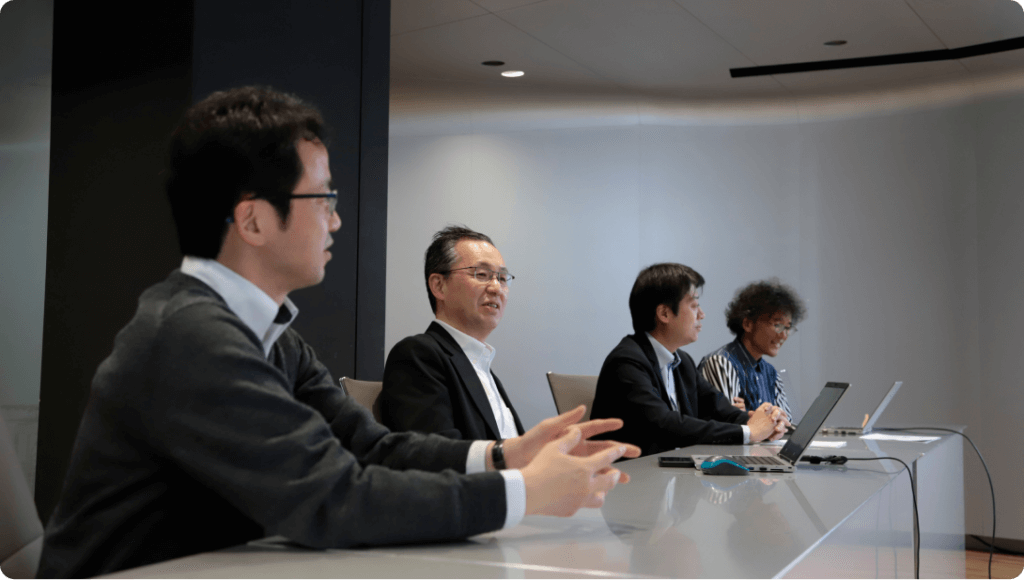
Mizuki Hayashi, Senior Chief Expert, Nagoya Branch, Product Department
Hideyuki Honda, Head of BIM Promotion, Design HQ
Satoru Andou, Senior Chief Engineer – Construction, Nagoya Branch
Eiichi Yoshioka, General Manager, Design Group 4, Nagoya Branch
Photo ©Tomohiro Tsukagoshi
Project: Port Messe Nagoya First Exhibition Hall 1
Project Location: Nagoya, Japan
Firm: Takenaka Engineering Co., Ltd., founded in 1610, established in 1909
President and CEO: Masato Sasaki
Project Type: Retail
Project Size: 40,716 sqm / 438,263 sqft
Year of Completion: 2022
Software used: Graphisoft Archicad, Solibri, Rhino, Grasshopper
Design BIM Tool Benefits
Download Takenaka’s diagram to find out how their Design Portal speeds up their work.
Project
Reaching new standards of sustainability
Designed to celebrate Port Messe Nagoya’s 50th anniversary, the Nagoya International Exhibition Hall is a landmark in the Japanese city of Nagoya, creating a new landscape by the sea.
Takenaka Corporation was commissioned to develop the exhibition hall and formed a joint venture with Kume Sekkei to deliver the project. The team designed and built a 20,000m2 column-free exhibition space with a wavy roof and dynamic glass façade, inspired by the sea and reflecting the landscape of the bay.
Meanwhile, the timber-lined interior creates a woody atmosphere, in a nod to the land’s historic role as a lumberyard during the construction of Nagoya Castle.
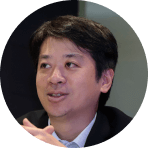
Photo ©Tomohiro Tsukagoshi
We were careful not to deviate from the design requirements, and we used all our manufacturing wisdom to ensure high constructability.”
Satoru Andou
Senior Chief Engineer, Construction, Nagoya Branch Work Station
Explore the Gallery
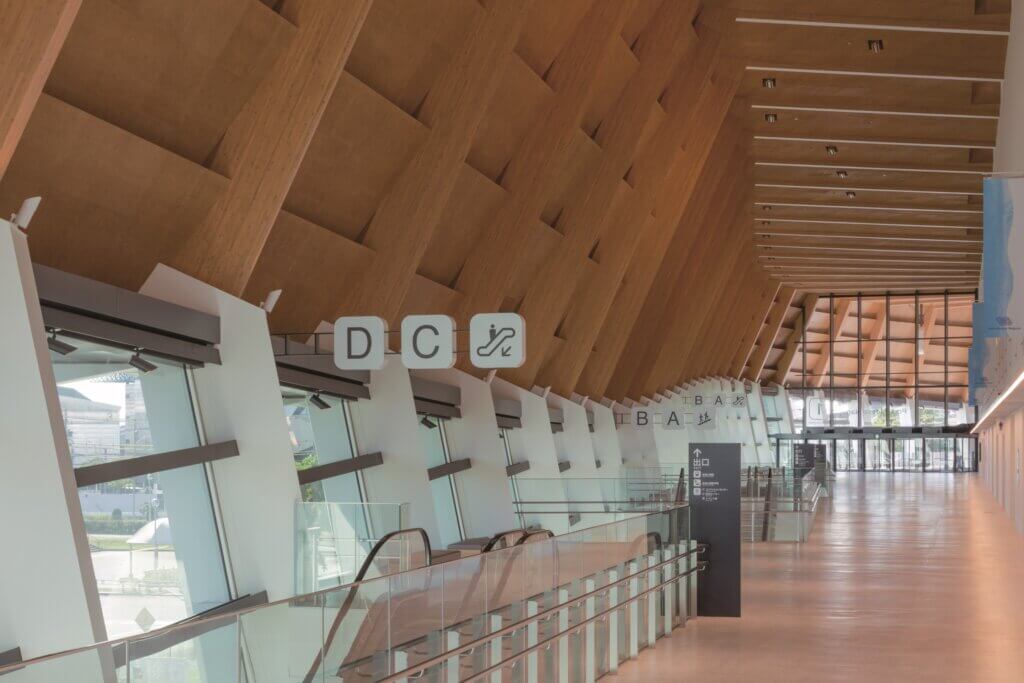
Port Messe Nagoya First Exhibition Hall, Takenaka Corporation, Japan, takenaka.co.jp, Photo: ©SS Co.,Ltd., Mitsunori Aiba
Design
Parametric model brings concepts to life
The team used design tools such as Rhinoceros and Blender to examine the conceptual volumes and shapes in the early stages of design. After deciding on a streamlined exterior with a wave motif, they used Rhinoceros and Grasshopper to take the concepts and organize them into a parametric model.
The designers imported these detailed components into Archicad and converted them into BIM elements. From the full Archicad model, the team generated 2D drawings and performed quantity calculations to inform the cost estimates for the project.
New to parametric design? Check out our self-paced online course, Get started with Parametric Design in Archicad. Learn to use the amazing capabilities of Rhino and Grasshopper to create parametric BIM models in Archicad.
Standardization
A complex façade
The project’s biggest challenge, both in design and construction, was the complex façade. With a polygonal shape, the top section is constructed from fire-resistant Moen-wood® while the lower section is made from steel.
The roof and walls of the façade were designed in modules to improve construction productivity. By unifying the joints of the structural Moen-wood and the steel frame, the length of each component, the angle of the joints and the position of the bending points could be standardized, improving productivity, quality and safety in construction.
Moreover, with standardization, the construction period could be easily calculated to improve production efficiency.
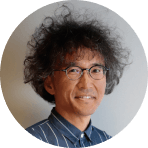
Photo ©Tomohiro Tsukagoshi
When you build a building this large, you necessarily need high production capacity. We thoroughly considered safe and efficient production methods, and managed to improve productivity by splitting the undulating roof and walls into approximately 70 units.
Eiichi Yoshioka
General Manager, Design Group 4, Design Department
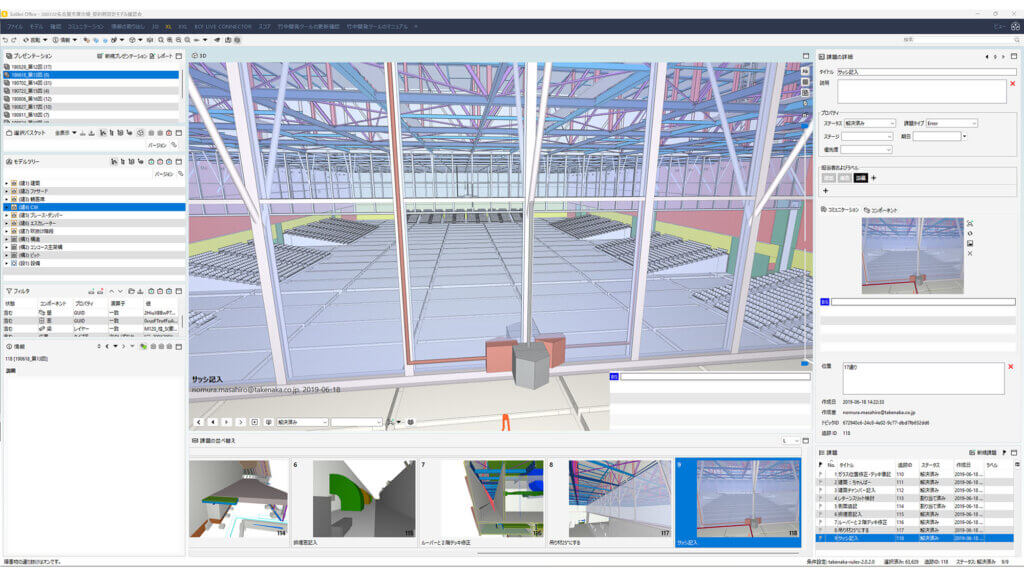
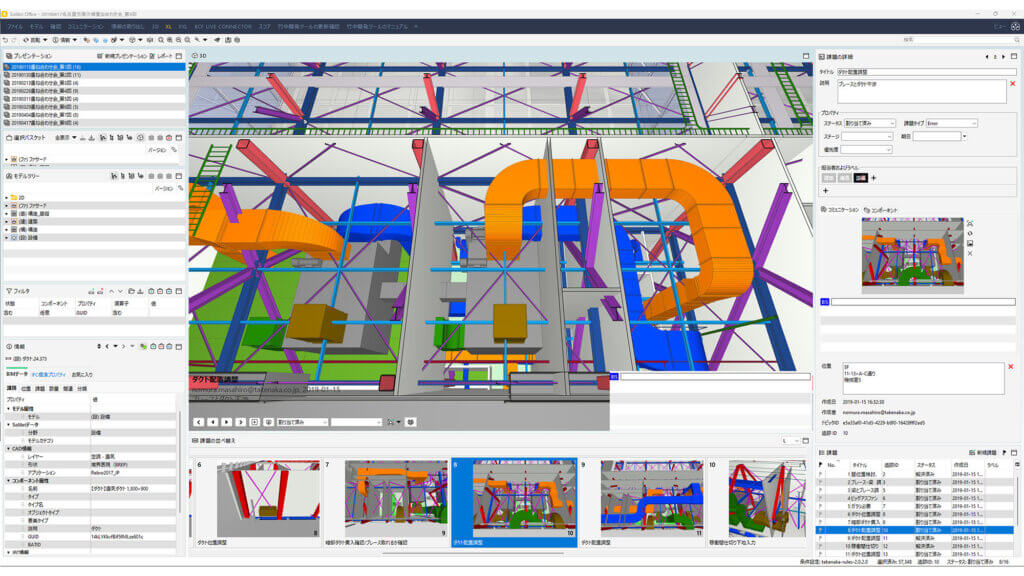
Provided by Takenaka Corporation
Collaboration
Solibri for clash detection
The interior of Exhibition Hall 1 is a pillarless area spanning 96 meters. A major challenge was to locate the ducts for the air conditioning and ventilation systems, electrical wiring, and water supply piping in this large 20,000 m2 space.
The 96-meter span structure is based on rigorous structural calculations and could not be modified. Working together, the design, construction and building services staff created accurate designs for the piping and wiring.
With these designs in place, the team undertook collision checks using Solibri. The Building Information Secretary staff, who perform BIM operator duties, immediately made modifications to the drawings, updating the 3D model in real-time.
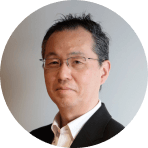
Photo ©Tomohiro Tsukagoshi
We use Solibri to check every project for compliance with the performance requirements.
Hideyuki Honda
General Manager, BIM Promotion Group, Design Division
Construction
A pre-construction mock-up
To address the challenge of creating a streamlined, polygonal façade, the team constructed a 1:1 mock-up. This enabled them to confirm the details of the complex steel joints and identify possible issues with construction.
By creating a mock-up, the team collected data for the actual construction, such as to confirm construction procedures and constructability, and were able to reflect this data in the construction plan and schedule.
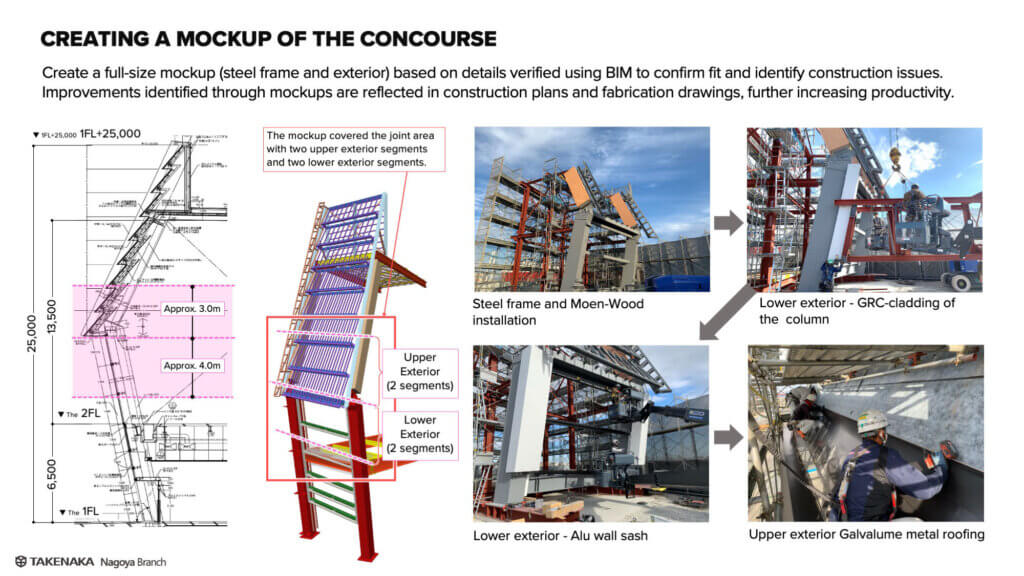
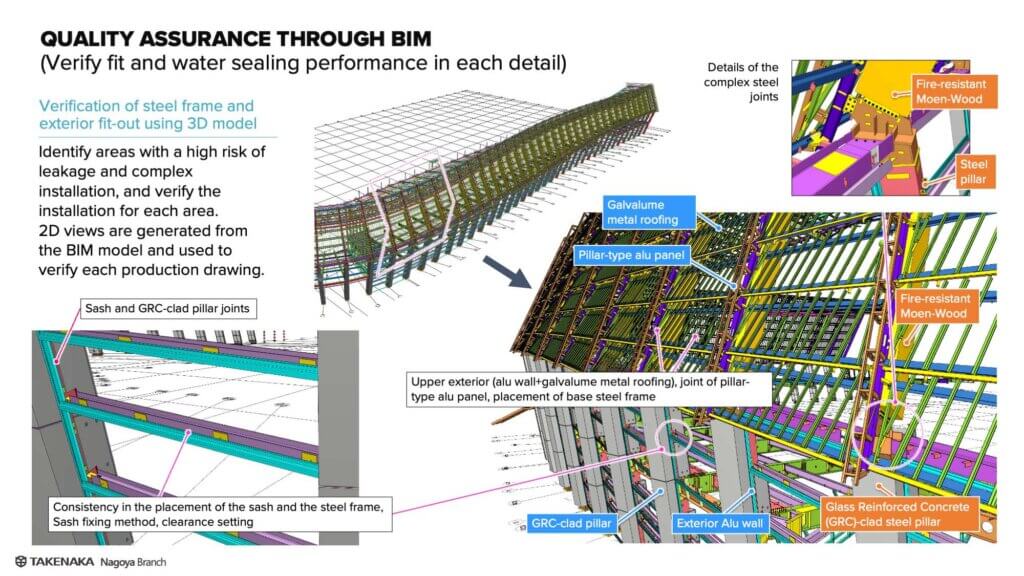
Provided by Takenaka Corporation
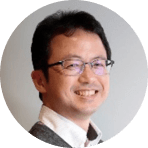
Photo ©Tomohiro Tsukagoshi
The jagged roof surface is made up of slightly twisted surfaces. With BIM, you can twist the material without applying force, but in reality, you won't know until you try it. Therefore, constructing a mock-up of the actual product can immediately resolve concerns on the construction side.
Mizuki Hayashi
Senior Chief Expert, Product Department, Nagoya Branch
Conclusion
The project was a success thanks to various innovations, such as improving productivity through modularization and ensuring safety during construction.
Takenaka’s focus on digital transformation and productivity reform is supported by BIM and data-driven business processes. By bringing together design and construction, Takenaka is pushing the boundaries of technological innovation.